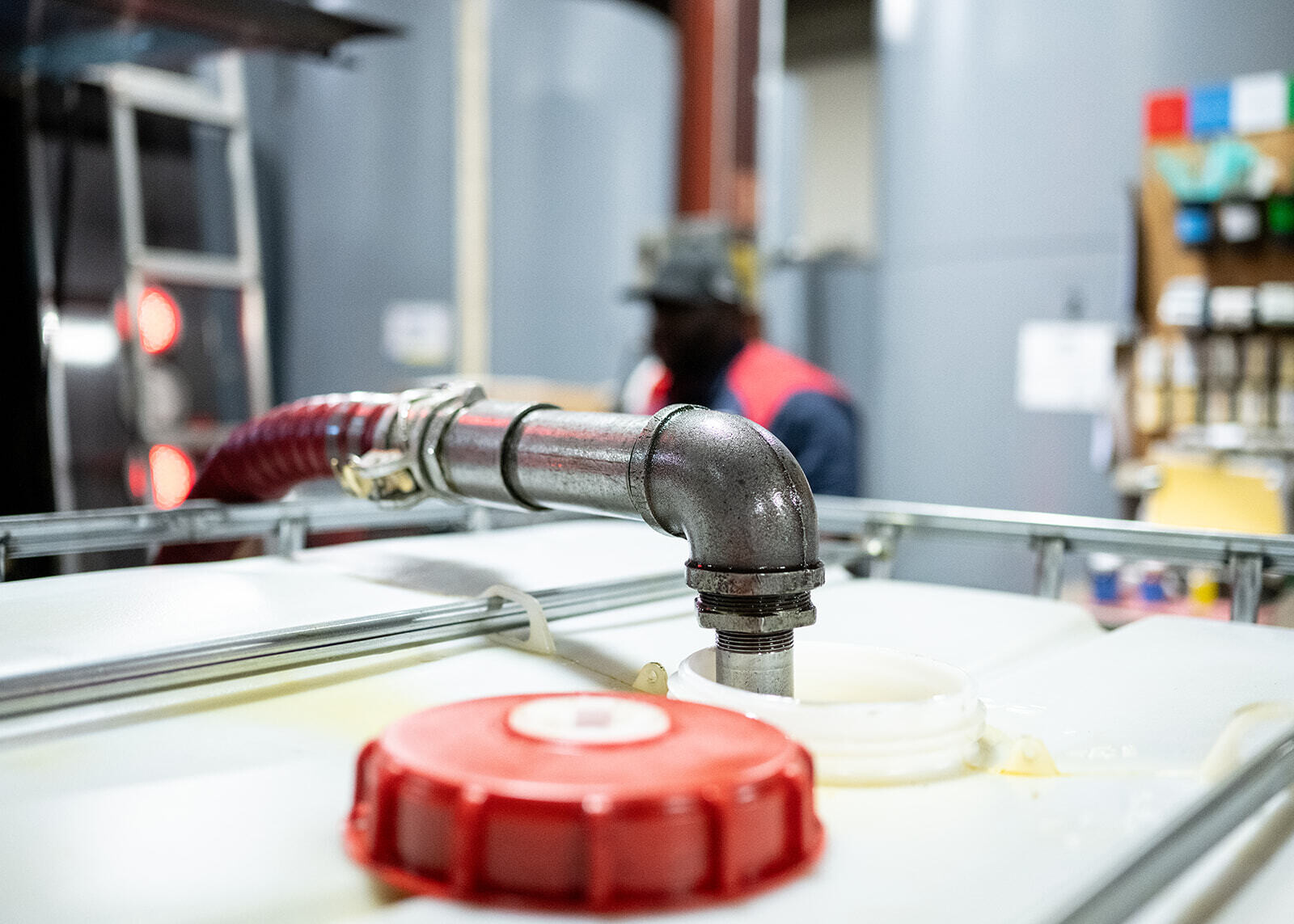
Most fleets rely on oil analysis—but not all of them do it well. A single test can catch early signs of wear, prevent unexpected failures, and extend oil drain intervals. But if you’re not sampling correctly or reading the results the right way, bad data leads to bad decisions.
Oil analysis is only as useful as the way it’s performed. The wrong sample location, inconsistent testing, or misinterpreted results can cause fleets to change oil too soon, replace components unnecessarily, or schedule service they don’t actually need.
This guide will show you how to get oil analysis right. With the right approach, fleets can maximize uptime, cut maintenance costs, and avoid the most common mistakes that lead to wasted time and money.
Why Oil Analysis Matters for Fleet Performance
Most fleet failures don’t happen overnight. Engines don’t just seize up out of nowhere, and components don’t wear out in a single day. The warning signs are there—if you know where to look.
That’s where oil analysis comes in. By tracking contamination levels, wear metals, and oil degradation, fleets can catch problems early, adjust maintenance schedules, and avoid costly surprises.
One of the biggest advantages of oil analysis is its ability to extend drain intervals safely. Instead of relying on fixed oil change schedules based on worst-case scenarios, fleets that monitor oil condition can go longer between changes—without risking excessive engine wear.
Oil analysis also reveals hidden failures in the making. High levels of iron, lead, or aluminum can point to bearing or piston wear before a breakdown occurs. Fuel dilution, coolant contamination, or excessive soot buildup often indicate bigger issues inside the engine—problems that would otherwise go unnoticed until it’s too late.
For fleets, the impact of oil analysis goes beyond just reducing oil changes. Catching these warning signs early prevents major repairs, minimizes downtime, and extends equipment life—all of which keep trucks running and revenue flowing.
How to Take an Accurate Oil Sample
Oil analysis is only as reliable as the sample itself. If the sample doesn’t accurately reflect the oil in the system, the test results won’t be useful—and that can lead to unnecessary maintenance or missed problems. To get reliable data, fleets need to take oil samples from the right location, in the right conditions, and with the right equipment.
1. Take the Sample from the Right Location
One of the most common mistakes fleets make is sampling from the drain plug. It seems logical—after all, that’s where the oil comes out—but that oil is loaded with settled debris that doesn’t reflect what’s actually circulating in the system. Taking a sample from the drain plug can trigger unnecessary repairs based on artificially high wear metal readings.
Instead, the best practice is to use a midstream sample port while the engine is at operating temperature. This ensures the sample reflects oil that’s actively lubricating engine components, giving a true picture of wear and contamination levels.
For the most consistent and contamination-free samples, fleets can install dedicated sampling valves, such as those available from Checkfluid. These valves allow technicians to take samples without opening the system, preventing dirt or moisture from entering and ensuring repeatable, high-quality results.
2. Avoid Sample Contamination
Even a small amount of dust, dirt, or moisture can throw off lab results. A contaminated sample can make perfectly good oil look like it’s failing—or worse, hide a real problem.
To prevent contamination:
Always use new, clean sampling bottles and tubing. Even a little leftover residue can distort results.
Flush the sample bottle three times before collecting the final sample. Fill it with oil, swirl it around, dump it out, and repeat twice more. This removes any residual contaminants before taking the test sample.
Never take samples from open containers or transfer oil between bottles before sending it to the lab.
Make sure the oil is at normal operating temperature when sampling to get an accurate viscosity reading.
3. Keep Sampling Intervals Consistent
A single oil sample is just a snapshot, but it’s the trend over time that tells the real story. Many fleet managers overreact to one bad report, assuming it means immediate action is needed. But unless it shows a catastrophic failure in progress, one sample isn’t enough to make a major decision.
The key is to test at regular intervals based on operating conditions, oil type, and manufacturer recommendations. Tracking patterns in wear metals, contamination, and viscosity shifts allows fleets to make smarter, data-driven maintenance decisions instead of chasing isolated numbers.
Interpreting Oil Analysis Reports – What to Look For
Once an oil sample is analyzed, the lab report reveals critical clues about engine condition. Interpreting these numbers correctly allows fleet managers to spot early warning signs and take action before a minor issue becomes a major failure.
Wear Metals – Signs of Internal Damage
Every moving part inside an engine experiences wear, but oil analysis can tell when that wear is accelerating beyond normal levels. Specific metals in the oil indicate which components may be failing:
Iron – Cylinder liner and crankshaft wear.
Copper & Lead – Bearing wear, often linked to high loads or oil contamination.
Chromium – Piston ring wear, potentially due to combustion inefficiencies.
Aluminum – Piston scuffing or excessive wear in aluminum components.
A gradual increase in wear metals over time is expected, but a sudden spike signals excessive friction, misalignment, or early-stage mechanical failure. If wear metal levels rise sharply between tests, fleets should investigate before a minor issue leads to unexpected downtime.
Fuel Dilution – A Red Flag for Injection Issues
Fuel dilution occurs when unburned diesel mixes with engine oil, thinning its protective film and reducing lubrication. While some fuel contamination is normal, excessive dilution indicates a problem inside the fuel system.
Common causes include leaky injectors, excessive idling, or incomplete combustion. If left unchecked, fuel dilution accelerates engine wear, shortens oil life, and leads to costly repairs. Fleets that see recurring fuel dilution in their oil reports should inspect their injectors, dosing systems, and combustion efficiency before small inefficiencies turn into expensive failures.
Coolant Contamination – A Sign of Bigger Problems
Coolant should never mix with oil. If an oil analysis detects glycol, sodium, or potassium, coolant is likely leaking into the system—often due to a failing EGR cooler, head gasket, or oil cooler.
Even a small coolant leak is a serious problem. Coolant contamination breaks down oil’s lubricating properties, leading to bearing failures, internal corrosion, and sludge buildup. If a leak is detected, fleets should act immediately to prevent catastrophic engine damage.
Oxidation & Viscosity Breakdown
As oil ages, it oxidizes, thickens, and loses its ability to lubricate. High oxidation levels usually point to excessive heat or oil that’s staying in service too long. This leads to sludge formation, increased viscosity, and poor engine efficiency.
Conversely, a sudden drop in viscosity suggests fuel dilution or shear thinning of viscosity modifiers, reducing the oil’s ability to protect metal surfaces. Fleets should track viscosity trends carefully—ignoring shifts in oil condition can result in premature wear and unexpected service needs.
Using Oil Analysis to Optimize Drain Intervals
One of the most significant benefits of oil analysis is the ability to safely extend oil drain intervals. However, this should be done based on actual oil condition rather than arbitrary mileage.
1. Why Fixed Drain Intervals Are Outdated
Traditional oil change schedules assume worst-case conditions, leading many fleets to replace oil that’s still performing just fine. Advances in high-performance oils like Mobil Delvac allow for longer service life, but the key is monitoring oil condition to ensure it’s still within spec.
Oil analysis provides real-time insight into when an oil change is actually needed, helping fleets avoid premature servicing while still protecting engine health.
2. Using Data to Adjust Service Schedules
Instead of relying on mileage alone, oil analysis allows fleets to:
Extend oil drains safely when analysis confirms the oil is still within spec.
Detect contamination early and adjust service schedules proactively.
Reduce waste by avoiding unnecessary oil changes.
3. Making the Switch to Extended Drain Intervals
Fleets looking to extend drain intervals need a structured approach:
Use a high-performance oil designed for extended drains (e.g., Mobil Delvac).
Implement a regular oil analysis program to ensure performance stays within limits.
Adjust intervals gradually instead of making a drastic change all at once.
Save Money Over the Long Haul With Correct Oil Analysis
Oil analysis isn’t just about checking whether the oil is still usable—it’s a powerful tool for catching early failures, optimizing drain intervals, and reducing maintenance costs. By following best practices for sampling, analyzing trends over time, and using high-performance lubricants, fleets can maximize uptime and reduce operating costs.
Want to optimize your fleet’s lubrication strategy? Contact GPI today to find out which high-performance Mobil Delvac™ oils best fit your maintenance goals.